产品设计对最终医疗设备的总体成本有很大影响。因此,具有丰富经验的医疗器械产品化服务机构在项目开始阶段往往会提前考虑产品的制造和设计问题,从而可以缩短产品开发时间,最大程度地降低开发成本并确保顺利过渡到生产中,从而加快产品上市时间。 下面我们谈谈在整个产品开发过程中降低诊断仪器成本的五种方式。
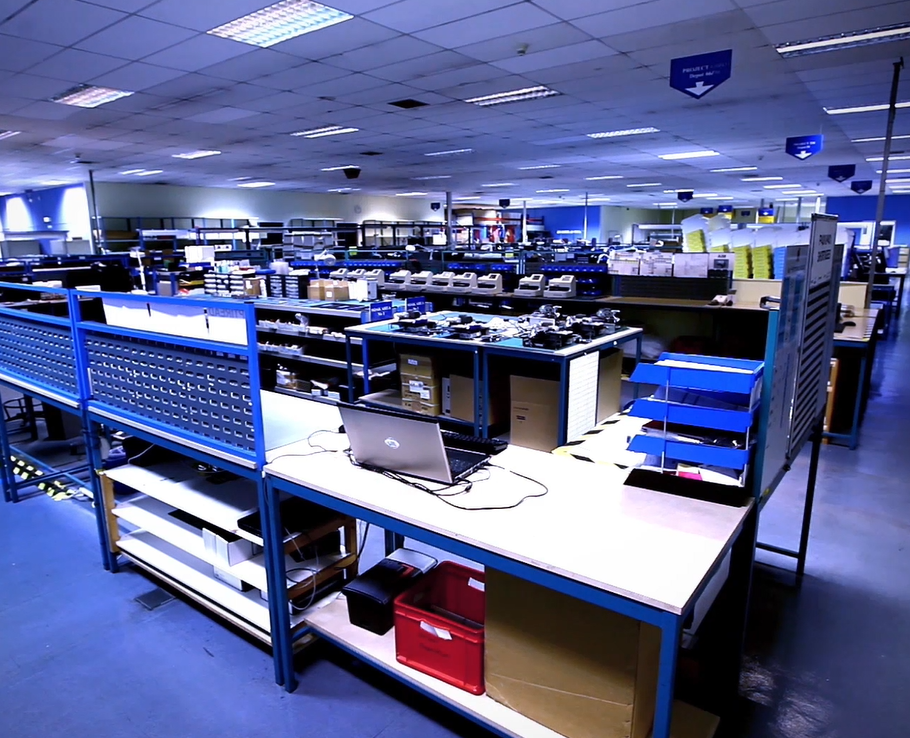
01
生产导向的产品开发
生产计划包括对流程的全面理解和落实,设计转移和制造方式工艺等内容。如果这项工作未能尽早着手,那么可能的返工将导致高成本的再投入和复杂的修改迭代。
从质量管控的角度来看,有效地将制造计划纳入到设计中能有效的降低成本投入。
因此,全面的,可实现的,以及可衡量的设计输入不仅可以保证仪器的顺利转化,还能节省返工所引起的人力,财力和时间。
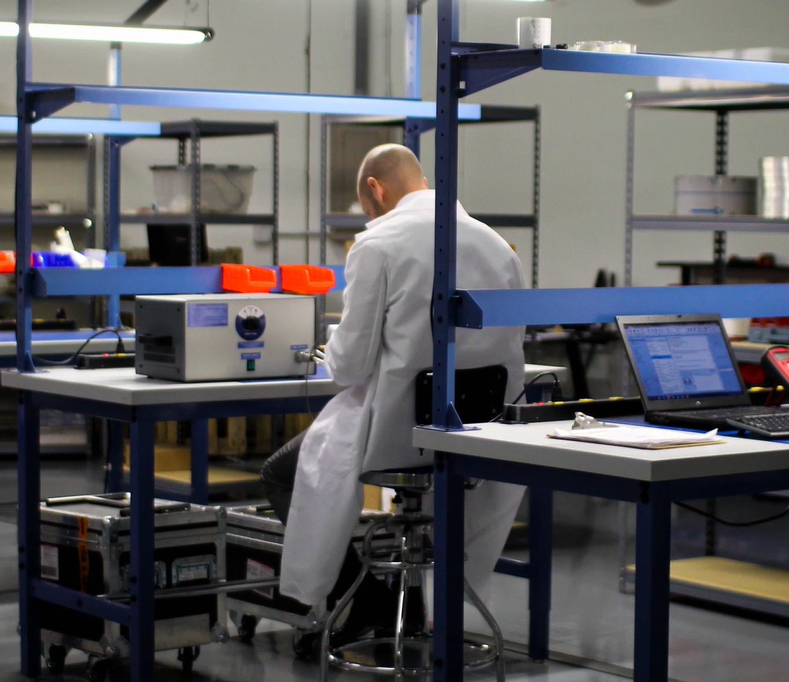
02
设计组装和可制造性
在开始详细设计之前,务必对产品概念进行严格评估,充分了解核心技术并估算所有成本。前期所有的分析为设计提供信息,还可能对制造成本产生重大影响。
我们遇到过产品由国外设计,国内生产的一些客户,这些产品设计非常新颖且复杂,但是国内生产能力有限而导致无法生产。
因此,在仪器开发过程中,制造工程师务必与设计团队确认项目可生产问题。
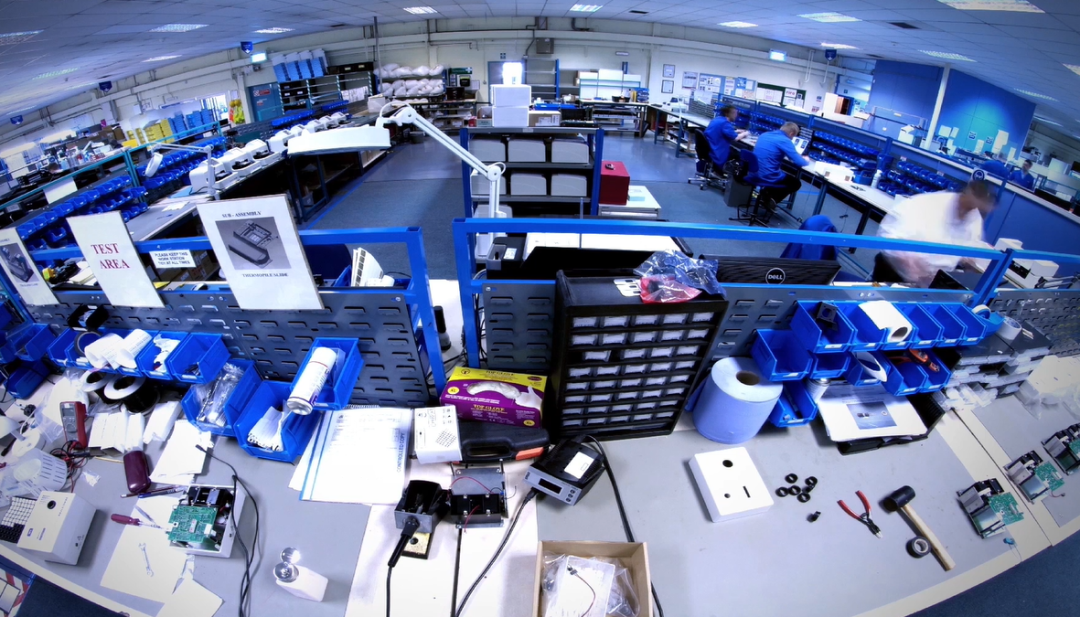
为装配而设计(Design for assembly-DFA)
为装配而设计(DFA)通过简化产品,从而降低装配成本。将DFA原理应用于产品设计可以有效提高产品的装配效率和降低装配的失误率,提高最终产品的质量和可靠性,有利于降低在制品和零件库存。
DFA可以被定义为一种改进产品设计的过程,以实现简便且低成本的组装,这可以通过同时关注功能和组装的双重性来实现。DFA在早期对零件和整个产品的设计进行分析,以解决任何组装问题,包括减少零件的数量,确保合理的组装顺序,设计只能以一种特定方式装配,减少生产时间的同时消除潜在的错误操作隐患。从而通过缩短整个产品的生命周期,降低成本。
可制造性设计(Design for manufacture-DFM)
在此过程中 ,制造工程师确保设计中的所有部件都能与最合适的和最具有成本效益的制造工艺相兼容。
关于可制造性设计我们在上篇中仔细探讨过定义和优势。DFM的具体任务随着生产过程的变化而变化。DFM意义主要包括:
比较设计方案,了解哪个方案的可制造性问题最少,生产成本最低。
确定不必要地驱动额外制造需求的设计特征。
确定仪器开发过程中的额外成本
确保在设计生命周期的后期不会出现制造问题。
生产过程的复杂性是行业很多仪器生产公司的痛点,现在利用先进的制造仿真工具让工程组织能够建立可靠的和可验证的DFM程序可以有效的完成生产成本的估算。
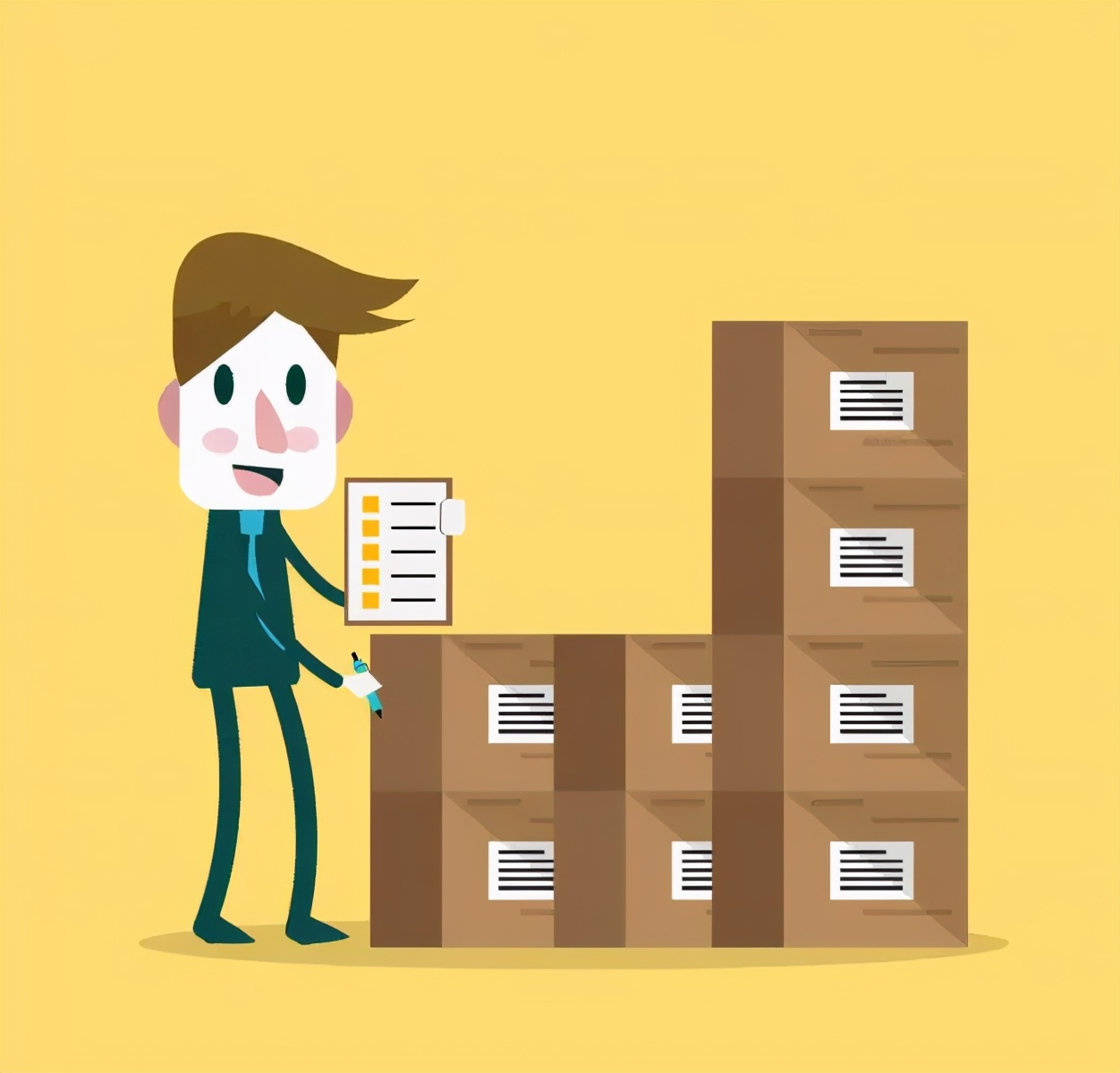
03
尽早建立供应链
供应链是个人,组织,资源,活动和参与产品或服务的生产和销售技术的连接的网络。供应链从原材料供应商到制造商的运输开始,到成品或服务到最终消费者的运输结束。
其中,对仪器生产成本影响较大的是物料成本。因此,在零件采购方面,对低成本与所需质量之间需进行平衡,选择供应商非常重要。
_
_
谨慎选择供应商
必须严格审查和选择供应商。
务必了解每个供应商为您提供的产品,确保他们可以正确地制造对应数量的组件。价格是如何构成的?公司文化是什么样的?他们的质量如何?他们是否采取积极措施来确保高质量的零件?
在可能的情况下,开发易于制造且不需要特殊工艺的零件。简化生产可以拓展潜在供应商的数量,从而更容易找到合适的供应商。
原材料成本在仪器最终价格中起到决定性作用。供应商虽然以最低价格供货,但是运输成本,关税和其他因素可能会影响这种优势。
供应商和材料在整个生产中起着重要的作用。参考资料和实地考察是缺一不可。
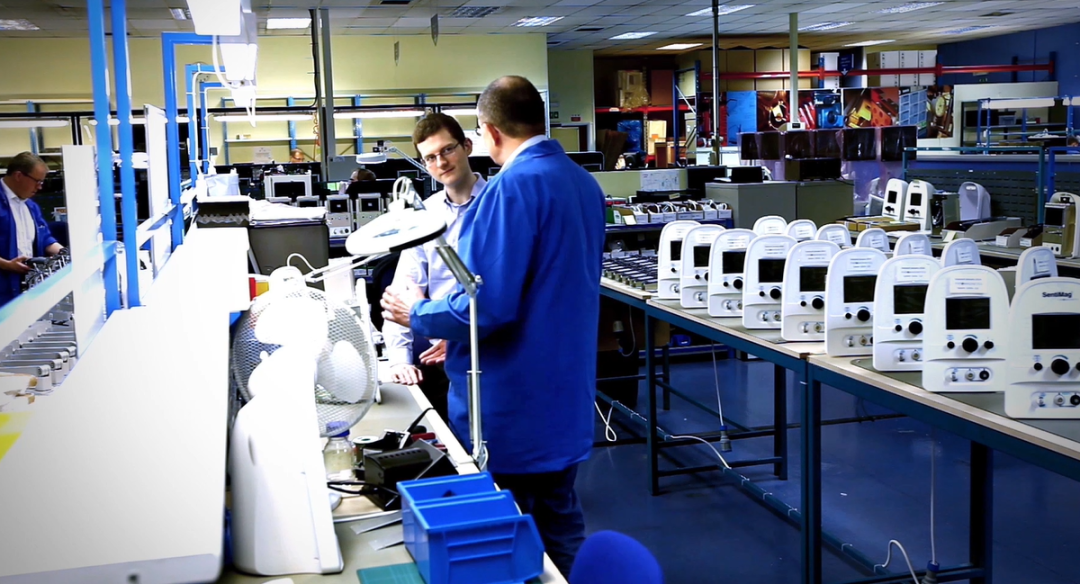
提前发现关键组件,以便对其进行管理
产品的关键组件对诊断仪器的功能至关重要,有些组件非常昂贵,并且在采购渠道和质量控制方面存在难点。尽早确定并建立这些组件的供应商对于降低成本,建立质量控制流程和按时交付时间非常重要。如果在生产过程中关键组件的供应问题可能会增加大量成本,则需要尽早寻找可能的替代解决方案。
在生产环境中,务必进行进货检查,避免劣质材料进入装配线。通过OEM制造商来采购零部件,不仅可以快速有效地建立完整供应链,而且可以建立完善的进货检验程序。
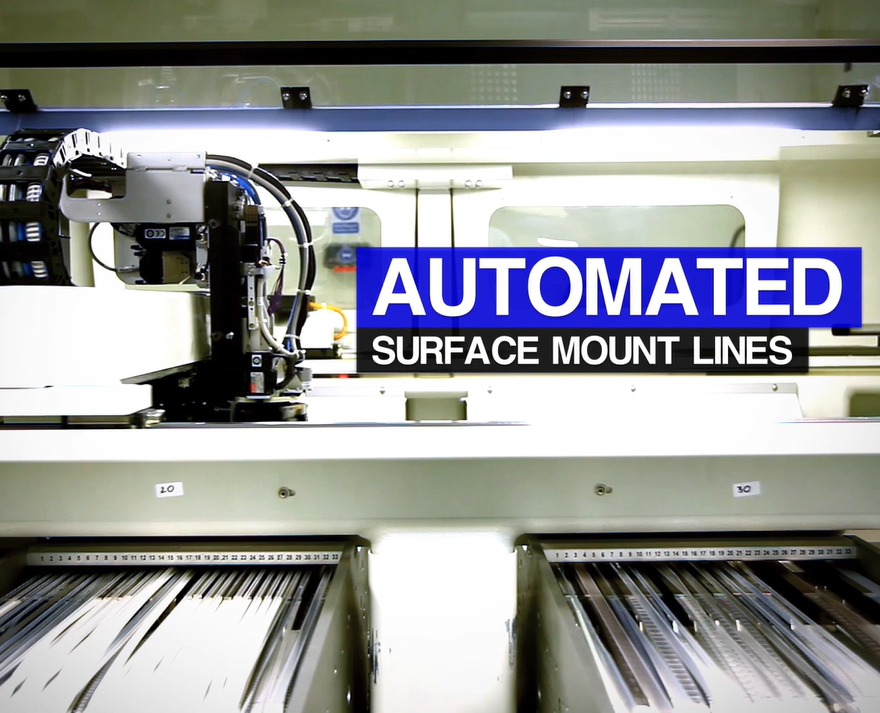
04
完善流程以提高质量和可重复性
提高生产过程的质量和效率
随着新产品开发过程的推移,它将最终进入正式的制造流程。大部分公司一般会等到设计阶段结束才开始制造过程,这种方式可能导致流程效率降低,质量问题增加,间接地增加产品生命周期的成本。因此在设计时考虑将生产过程可用于多个原型构建,让设计和制造团队可以在开发阶段就以使用现有生产过程为目的,并通过迭代来完善过程。这种方法可以提高质量和效率,并实现可观的持续成本节省。
通过分析流程失效来提高质量和可重复性
通过流程失效模式可以识别流程中潜在的质量风险,并根据严重性和发生程度对这些风险进行优先级排序。从而让开发团队可以专注最重要的项目,并在可能的情况下消除设计中潜在的质量问题。通过仅在需要修改的部分上进行设计工作,最大程度地减少组装线上返工或报废的可能性,从而降低了开发和生产成本,同时降低了制造过程中的复杂性。
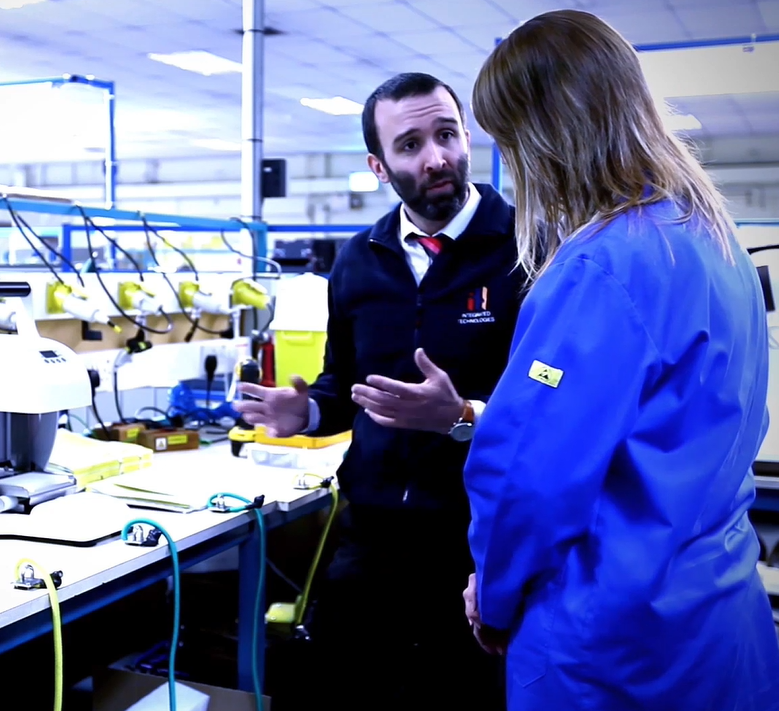
05
集成设计和制造团队的优势
当设计,工程和制造团队在同一个环境下工作可以避免很多问题。以下是整合团队的一些优势:
在正确的时间提供正确的建议。
整合制造工程师和设计团队可以快速做出决定。同时可以在可制造性方面引导开发。
可以立即转移到制造。
利用已建立的沟通渠道,标准化文档格式和共享流程的团队,可以大大缩短准备时间,以便在开发和生产之间进行无缝转换。
单点责任制。
在转移和建立过程中发生了责任和所有权的移交。拥有一支完整的团队可确保问责制,并且在生产开始之前,团队可以解决任何潜在风险。此外,在项目建立过程中,拥有一名与开发团队一起工作的制造工程师是建立制造过程的重要一环。
从产品开发过程开始就为制造做准备,设计有效的制造工具,尽早建立供应链有助于产品的可制造性。严格的项目计划,集成设计,工程和制造团队的过程是提高效率并最终降低诊断仪器成本的关键。
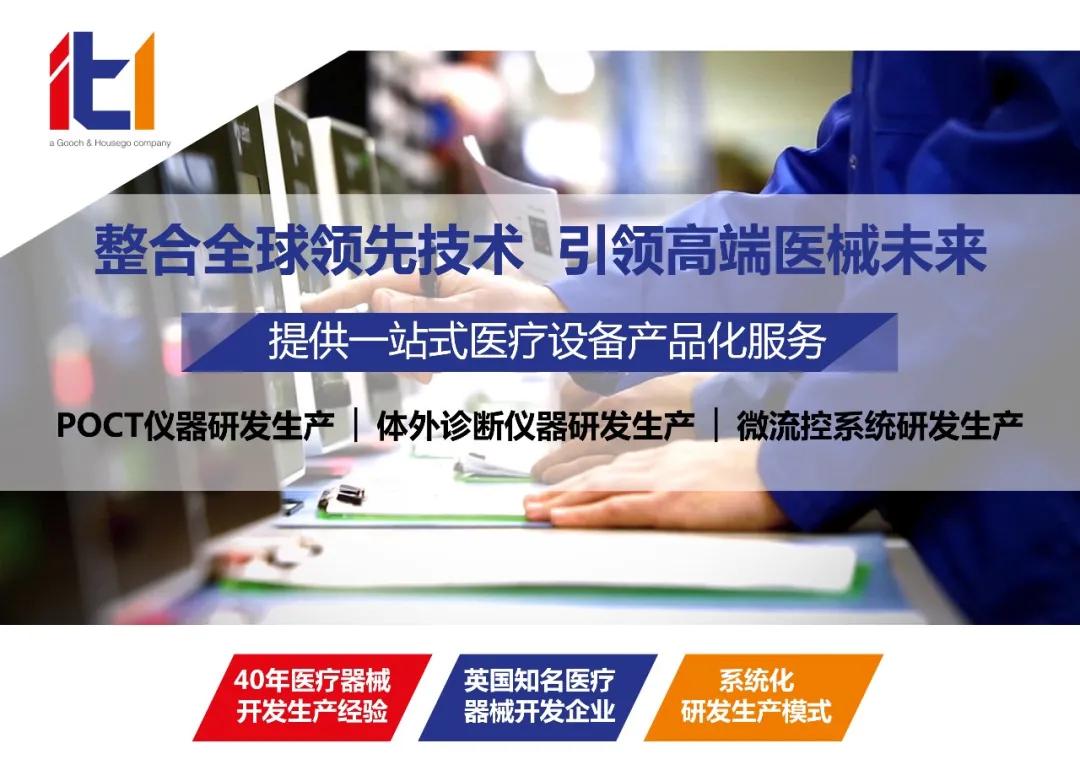
ITL专注体外诊断仪器的设计生产,拥有行业领先技术,在英国,美国和中国设立工厂,使用先进的设计开发流程,专业的智能生产配备,完善的质量管理,健全的产品检测制度,强大的人力资金资源,成熟的供应链体系,ISO13485和ISO9001质量管理体系对生产制造和质量管控进行实时动态管理,为客户提供一站式的服务。
|